港珠澳大桥正破世界级难度 基槽精挖犹如海底绣花(2)

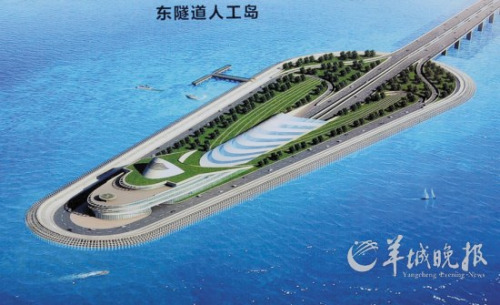
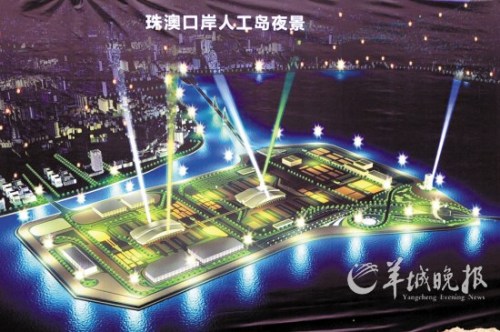
探寻挖泥船
基槽精挖犹如海底绣花
误差:0-0.5米!在茫茫伶仃洋的海底开挖5.6公里的隧道,这个误差绝对属于“精密”,如海底绣花一般。因此,港珠澳大桥海底沉管隧道基槽被称为世界上同类工程中难度最大的。
港珠澳大桥为桥隧岛一体化交通集群项目,从粤港分界线到珠澳人工岛的30公里是大桥的主体工程,其中就包括了桥、岛和 5.6公里的海底沉管隧道。该隧道从珠江主航道下穿过,已于去年1月开始开挖基槽,至今完成总工程量的55%。中交广航局相关负责人说,“精”是这项工程的关键词。“高质量标准的隧道基槽精挖,就如同海底绣花。”
负责“绣花”的是中交广航局的两艘挖泥船“广州号”和“金雄”。3月21日,羊城晚报记者随港珠澳大桥岛隧工程部相关负责人先后到这两艘船上。记者在“广州号”看到,两个巨型耙头从海里缓缓提升至海面,通过粗黑管与船上的泥仓相连,泥仓里不断有多余的海水被排出。“广州号”边吸泥、边航行,由置于船舷的耙头松土、吸入泥浆,通过管路把泥浆传送到船中设置的开底泥舱,经沉淀后把泥水分离。
船长龙真健说,“广州号”40分钟就能装满5250立方米的泥,但随后需航行30海里到大万山岛倾倒,来回得花上5、6个小时,所以一天大概只装3船左右。据介绍,“广州号”主要用于港珠澳大桥沉管隧道基槽的粗挖。
另一艘基槽开挖作业船“金雄”是抓斗式专用精挖船,往海底抛锚固定船身后即原地作业,4条粗钢丝把9米高、110吨重的抓斗从海底拉起后,泥浆被倾倒在预备好的载泥船上后再运走。在船上的控制室,船长向记者展示了“金雄”的精挖武器———平挖控制箱,里面是精密的集成器。
船长唐少鸣说:“即使有风浪,控制器也可以根据船的状态调整下挖深度,因此‘金雄’本身受外力影响不大,问题是载泥船会因为风浪太大而不稳,因此一般来说7级风以内才可以作业。”
探访沉管工厂
每段沉管都仿如一座别墅
今年2月27日,历时14个月的港珠澳大桥岛隧工程沉管管节预制工厂在桂山牛头岛正式建成开厂。
该厂是迄今世界最大的沉管预制厂,港珠澳大桥沉管隧道所需的33段管节都将在此通过大型现代化、工厂化的生产线预制而成。预计今年5月将正式预制第一节沉管。
港珠澳大桥近6公里长的海底沉管隧道共由33段沉管组成,每段沉管都仿如一座别墅,全部采用预制的方式。
如此大的别墅如何预制?又怎样运到施工现场?羊城晚报记者近日登上珠海桂山牛头岛,探访这座刚刚建成的生产车间。
沉管预制“世界级难度”
在牛头岛崭新的钢结构厂房中,并列着两条巨型管节的生产线,均已完成安装调试。据了解,港珠澳大桥沉管隧道每个180米长标准管节由8个节段组成,每节长22.5米、宽37.95米、高11.4米、重达7.4万吨。它们都将在该厂通过大型现代化、工厂化的生产线预制而成。
相关负责人说,港珠澳大桥设计寿命是120年,这要求沉管不能有任何缺陷,预制过程中一个小环节出错都足以让整段沉管报废。港珠澳大桥主体工程设计联合体的设计总负责人孟凡超曾告诉羊城晚报记者:“预制一个小件很容易,预制如此庞大的混凝土,要防止它有裂缝这就具有世界级的难度。”
两小时检测一次含水率
港珠澳大桥如何保证它的原材料不是“豆腐渣”?沉管预制厂第一分厂高级工程师周光强说,除了沉管的外形尺寸要控制在5毫米以内的误差外,混凝土的取样检测也十分重要。
经过两年时间的研究,混凝土的配合比达到了沉管预制的要求。目前,沉管预制厂配备了自己的试验室,600多平方米的试验区设有10多个样品检测室。到了正式生产沉管的时候,每隔2-3个小时就要检测一次沙石中的含水率,据此设定参数调整混凝土配比,然后在搅拌站具体调控。
花上3年才能送到目的地
据称,将预制好的沉管全部从牛头岛运到港珠澳大桥的隧道沉放区要3年时间,这令人万分不解,这段距离也就7公里,为什么要这么长时间?
高级工程师周光强说,沉管浮运受天气因素影响较大,从浮运到沉放需要连续72小时的良好天气,这需要提前通过气象窗口预报,保守估计浮运和沉放一节沉管需要一个月的时间,预计要到2015年才可以完成所有沉管的安装。
背景资料
港珠澳大桥主体建造工程于2009年12月15日上午开建,该桥总投资超700亿元,设计使用寿命120年,将于2016年完成。大桥主体工程采用双向6车道的桥隧结合方案,全长约29.6公里,海底隧道长约6余公里,并修建东、西两个人工岛提供桥隧转换设施。
率先动工的部分为珠澳口岸人工岛填海工程。它分为护岸工程、陆域形成、地基处理等单位工程。目前东南护岸堤身工程基本完成,陆域形成工程已完成,岛内区平均标高约2米,岛壁区标高约3米。近期施工项目主要以地基处理施工为主,至今累计完成投资约11.6亿元。(记者 梁卓慧)
>国内新闻精选:
